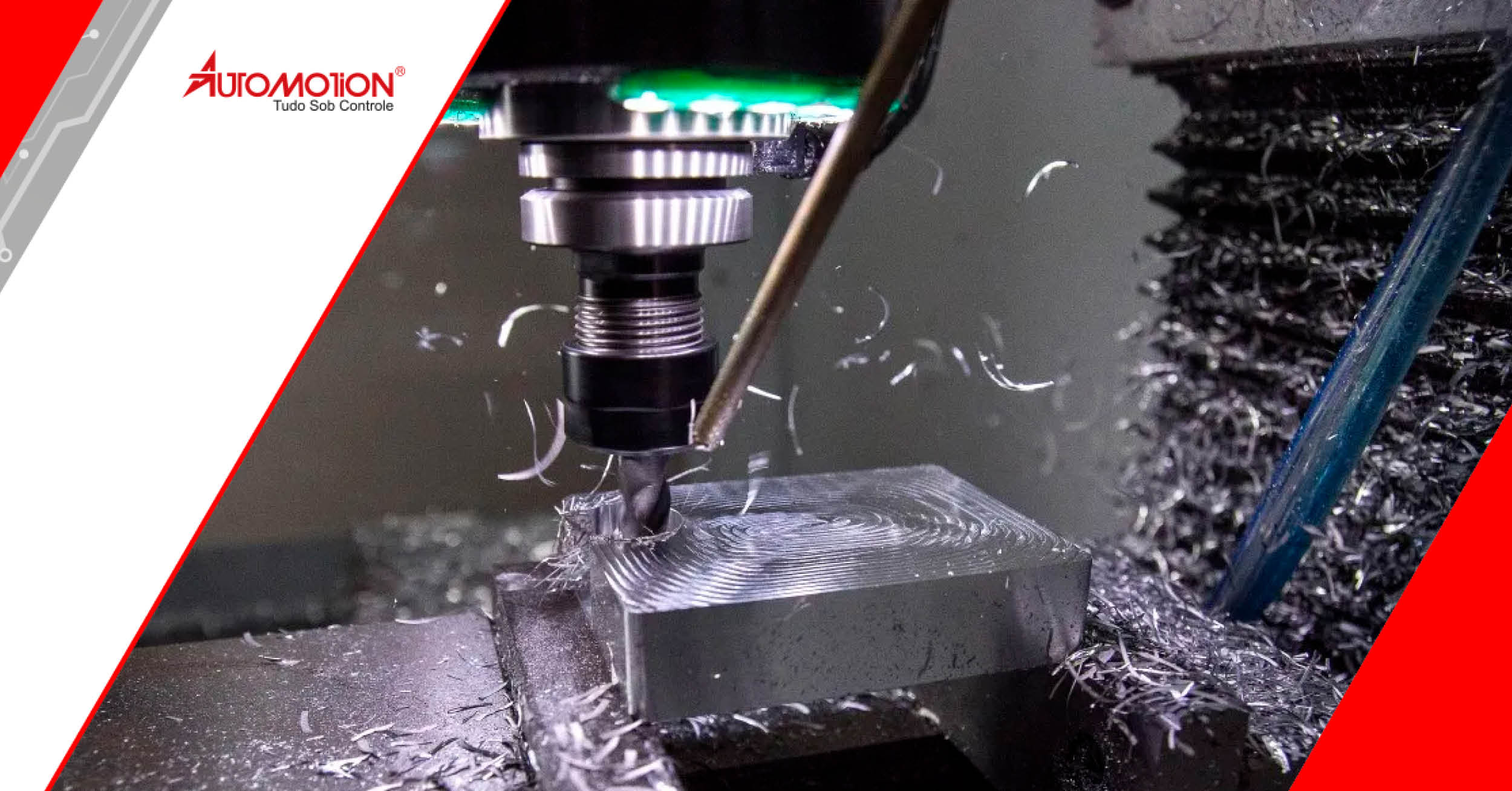
FA.6.91.EN Trabalhar sob eixos verticais – mas com segurança!
Freios de segurança para a proteção eficiente de pessoas e máquinas. Os eixos verticais apresentam muitos riscos em sua operação, principalmente quando o trabalho deve ser realizado diretamente abaixo deles. Portanto, um sistema confiável para a proteção de máquinas-ferramentas e colaboradores é mais que necessário: é fundamental. Com a instalação de freios de segurança adicionais, estes riscos podem ser resolvidos de forma eficiente e econômica – graças a diversos princípios funcionais e formas de construção, também é possível adaptá-los para máquinas que já estão em operação. Combinado ao monitoramento e controle inteligente de freios, a transmissão de potência mayr® torna as máquinas-ferramenta seguras e adequadas para as especificações da Indústria 4.0. Seja em uma falha na máquina-ferramenta, que deve ser corrigida rapidamente, ou simplesmente no carregamento de uma máquina com uma nova peça de trabalho – a operação diretamente sob os eixos verticais é frequentemente inevitável. A situação muitas vezes causa grande desconforto, e a preocupação não é completamente infundada: no caso de eixos carregados por gravidade, há sempre um risco potencial de que a carga caia ou se movimente sem controle. Por isso, é importante que o fabricante da máquina realize uma análise de risco para os eixos críticos de segurança durante o planejamento, além de determinar o Nível de Desempenho (PL) necessário de acordo com a norma DIN EN ISO 13849-1 (EUROPA) e NR12 (BRASIL). O objetivo é eliminar permanentemente a queda precipitada ou descontrolada da carga, nos quais as distancias longas de frenagem não são permitidas. Os fabricantes se deparam, desta maneira, com o desafio de garantir toda essa segurança, ao mesmo tempo em que criam um design eficiente, resistente e econômico. O uso de freios de segurança adicionais representa uma medida eficiente para atender a todos esses requisitos. Eles já podem ser planejados durante a construção, mas mesmo os sistemas existentes podem ser facilmente adaptados para oferecer toda esta segurança na linha de produção. Para isso, a mayr® powertransmission oferece uma ampla gama de freios de segurança extremamente confiáveis e especialmente desenvolvidos para a proteção de eixos carregados por gravidade. Nunca comprometa a segurança Os freios funcionam de acordo com um princípio à prova de falhas, com travamento na condição desenergizada. Desta forma, eles também podem fornecer segurança suficiente em situações críticas, como uma parada de EMERGÊNCIA ou uma falha de energia. Além disso, apenas materiais de reconhecida eficiência e testados são usados, garantindo total eficácia e segurança, em todos os momentos da operação ou nas paradas, sejam elas programadas ou não. Um fator importante para a seleção do freio é a situação de instalação na máquina-ferramenta. Dependendo da construção, existem diferentes possibilidades para a integração ou adaptação de freios de segurança. Uma posição possível encontra-se diretamente entre o servomotor e o fuso. Com o sistema de freio ROBA®-topstop®, a mayr® powertransmission é capaz de oferecer um módulo independente que segura o eixo vertical de forma confiável em qualquer posição, mesmo que o motor tenha sido desmontado para fins de manutenção ou transporte. O eixo não precisa mais ser suportado, acelerando substancialmente o processo de substituição do motor de acionamento. Dessa forma, os custos são reduzidos e os tempos de parada para reparos são muito reduzidos. Com suas dimensões de flange adaptadas, o freio pode ser facilmente integrado mesmo em projetos já montados. O freio de segurança atende aos altos padrões IP e atualmente está disponível até a proteção IP65, ou seja, já está bem protegido contra a penetração de graxas ou névoa de óleo. Uma inspeção voluntária do protótipo através do Deutsche Gesetzliche Unfallversicherung (Seguro Estatutário de Acidentes, DGUV) confirma que o dispositivo de frenagem é um “componente testado e comprovado” em termos de categoria 1 de acordo com a norma DIN EN ISO 13849-1 e NR12. Freios lineares confiáveis, também para fins de retrofit O freio linear ROBA®-linearstop funciona independentemente do motor de acionamento, atuando em uma haste de freio separada e também oferecendo o máximo em segurança. A forma de construção compacta permite uma integração rápida em máquinas e sistemas já existentes. O freio linear ROBA®-linearstop está disponível para projetos eletromagnéticos, hidráulicos e pneumáticos. Todos os freios lineares da mayr® powertransmission são adequados para ações de frenagem de parada de emergência. Aversão pneumática também foi inspecionada e confirmada como um dispositivo de frenagem dinâmica de qualidade total pela TÜV (Inspetoria Técnica Alemã). O ROBA®-pinionstop é um freio de segurança de abertura eletromagnética com pinhão apoiado por rolamento integrado. É, portanto, interessante se não houver hidráulica ou pneumática disponível ou se não houver sido planejada por algum motivo. Este freio também funciona independentemente do motor e é especialmente projetado para eixos com acionamentos de cremalheira. O pinhão integrado trava diretamente na haste dentada, sempre que necessário, e pode ser adaptado a sistemas existentes. A fixação direta nas massas a serem travadas tem,na maioria das vezes, uma vantagem importante: os elementos de acionamento entre o motor e a massa móvel como fusos, porcas de fuso, acoplamentos de eixos ou engrenagens não influenciam os níveis de segurança. E é exatamente isso que o freio de segurança ROBA®-guidestop faz: ele é integrado a um carro e, juntamente a dois circuitos de freio independentes, prende diretamente na guia do trilho perfilado, sem folga e com alta rigidez. O ROBA®-guidestop atua com perfeição mesmo em casos de parada de emergência ou falha de energia, freando a carga do movimento dinâmico até a parada. Tecnologia de freios 4.0 – o futuro do monitoramento As palavras-chave da Indústria 4.0 são evolução e controle. Neste sentido, o objetivo é mapear todos os processos digitalmente. Os dados assim coletados formam a base para processos inteligentes de planejamento, produção e fluxo de mercadorias. Mas a manutenção preventiva ou mesmo modelos de negócios completamente novos também devem se mover nesse sentido. Sob essas demandas, as exigências impostas ao monitoramento dos freios de segurança também estão aumentando. Nesse ambiente, o sistema de monitoramento de freios sem contato já se estabeleceu como padrão e funciona de forma totalmente confiável. Com o módulo ROBA®-brake-checker, a mayr® powertransmission…
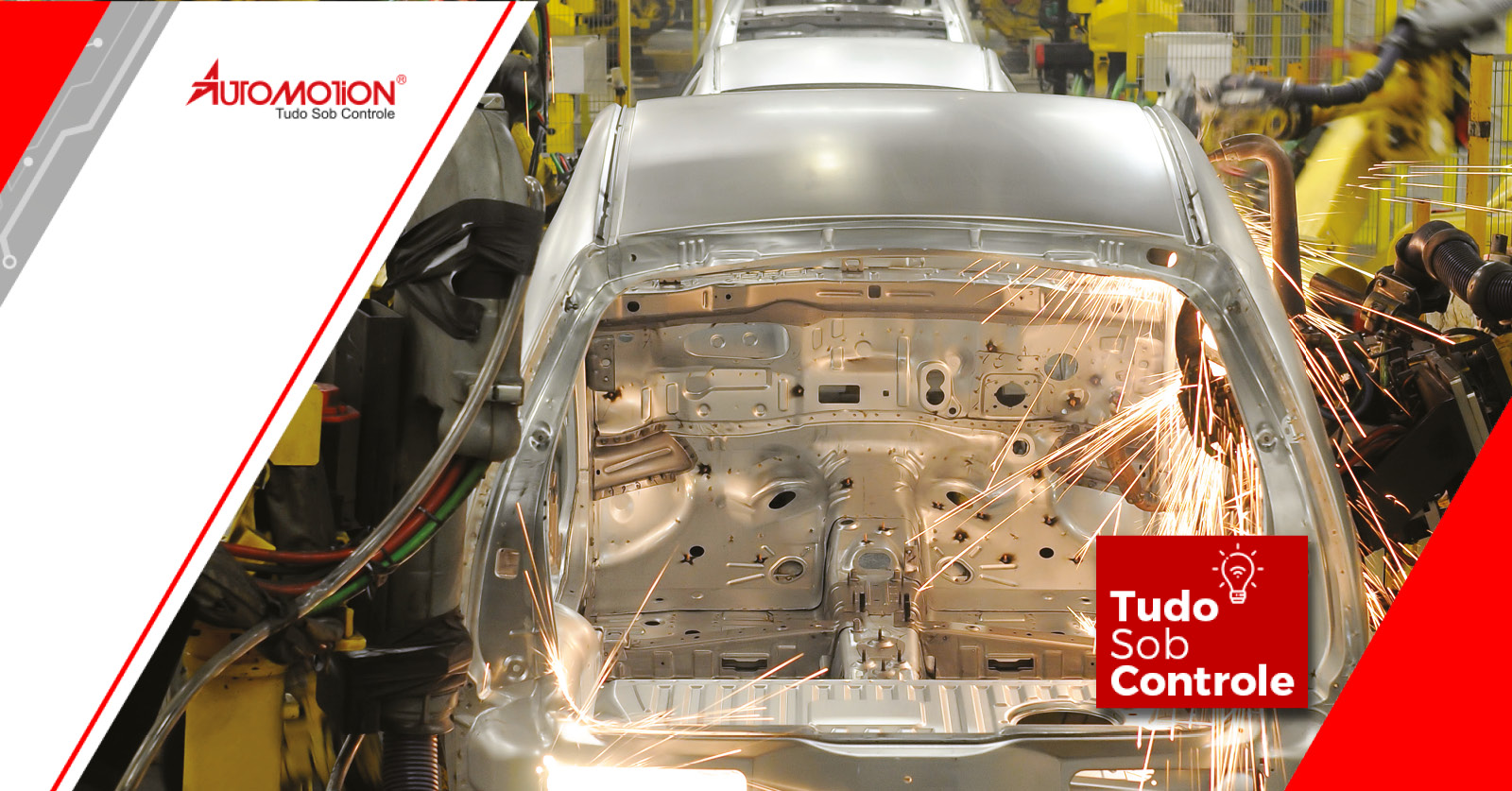
SOLDA PONTO
GTW – A Mais Recente em Atuação para solda ponto. GTW é a última palavra da Exlar® em atuadores para robôs de solda em linha de produção: mais uma verdadeira revolução da marca, que vai conquistar seu espaço na indústria, por meio da qualidade, da durabilidade e da precisão. O GTW é construído a partir da base da já reconhecida série de atuadores GS, que revolucionaram o cenário dos atuadores eletromecânicos e estão presentes em milhares de indústrias em todo o mundo, desde 2006, com mais de 25.000 unidades vendidas em aplicações para soldagem automática. A Série GTW garante às indústrias soluções flexíveis aliadas a recursos de baixa manutenção e durabilidade comprovada. O atuador GTW dá continuidade ao desempenho excepcional dos produtos da plataforma Exlar GTX da Curtiss-Wright e incorpora projetos para atender aos principais fabricantes globais da indústria automotiva. O motor/atuador GTW pode ser integrado a controladores de robô ABB, Comau, Fanuc e KUKA, assim como a controladores de acionamento de 7 eixos Bosch Rexroth e Festo. Em breve, poderão ser também conectados a Interfaces Yaskawa, Nachi e Kawasaki. Quem é a Exlar®? A Exlar® fabrica atuadores lineares de roletes eletromecânicos, servomotores rotativos e soluções de controle integrado para uma ampla e variada gama de aplicações. A tecnologia exclusiva da marca possibilita uma substituição elétrica eficiente para cilindros hidráulicos ou pneumáticos, além de também garantir mais robustez e confiabilidade para fusos de esferas. Com forças de até 80.000 libras e velocidades de até 60 polegadas por segundo, as soluções da marca são capazes de fornecer maior força e velocidade em dimensões reduzidas, quando comparadas à outras tecnologias de atuação de capacidade semelhante. Os atuadores Exlar ® têm mais flexibilidade, maior eficiência e menor necessidade de manutenção do que as soluções hidráulicas e pneumáticas tradicionais. Seja para aumentar a produtividade ou reduzir o custo total de propriedade, nossa equipe de engenheiros altamente qualificados pode montar a solução perfeita para suas necessidades! Benefícios GTW Conectividade para atender às especificações do drive, incluindo interface com os principais robôs industriais automotivos, com conexão rápida e fácil. Dispositivo de feedback e alinhamento para atender às especificações do fabricante do drive, incluindo controladores de robô KUKA, ABB, Comau e Fanuc, bem como controladores de acionamento de 7 eixos Bosch Rexroth e Festo. Mais de 20 milhões de perfis de solda típicos. Recursos de montagem integrados para a prática adaptação a uma variedade de configurações de pistola de solda. Dois tamanhos de quadro disponíveis para atender a quase todas as necessidades. Integração com os sistemas C-Gun, X-Gun e Pinch. Robustez, confiabilidade e durabilidade: redução do tempo de inatividade e maior produtividade. Seu design modular garante facilidade de personalização aparafusada em campo. Maximizando a vida útil | Minimizando a manutenção Os atuadores da série GTW oferecem benefícios nas situações onde os contaminantes estão presentes em aplicações de soldagem por pontos. Os designs especiais, tanto da vedação, quanto do limpador, evitam que contaminantes se infiltrem nos componentes mecânicos e elétricos do motor. Estes designs exclusivos e cuidadosamente pensados minimizam o tempo de parada para manutenção, maximizando a eficiência e a vida útil dos componentes do fuso de rolos invertidos durante os milhões de ciclos de trabalho necessários para garantir inigualável produtividade.
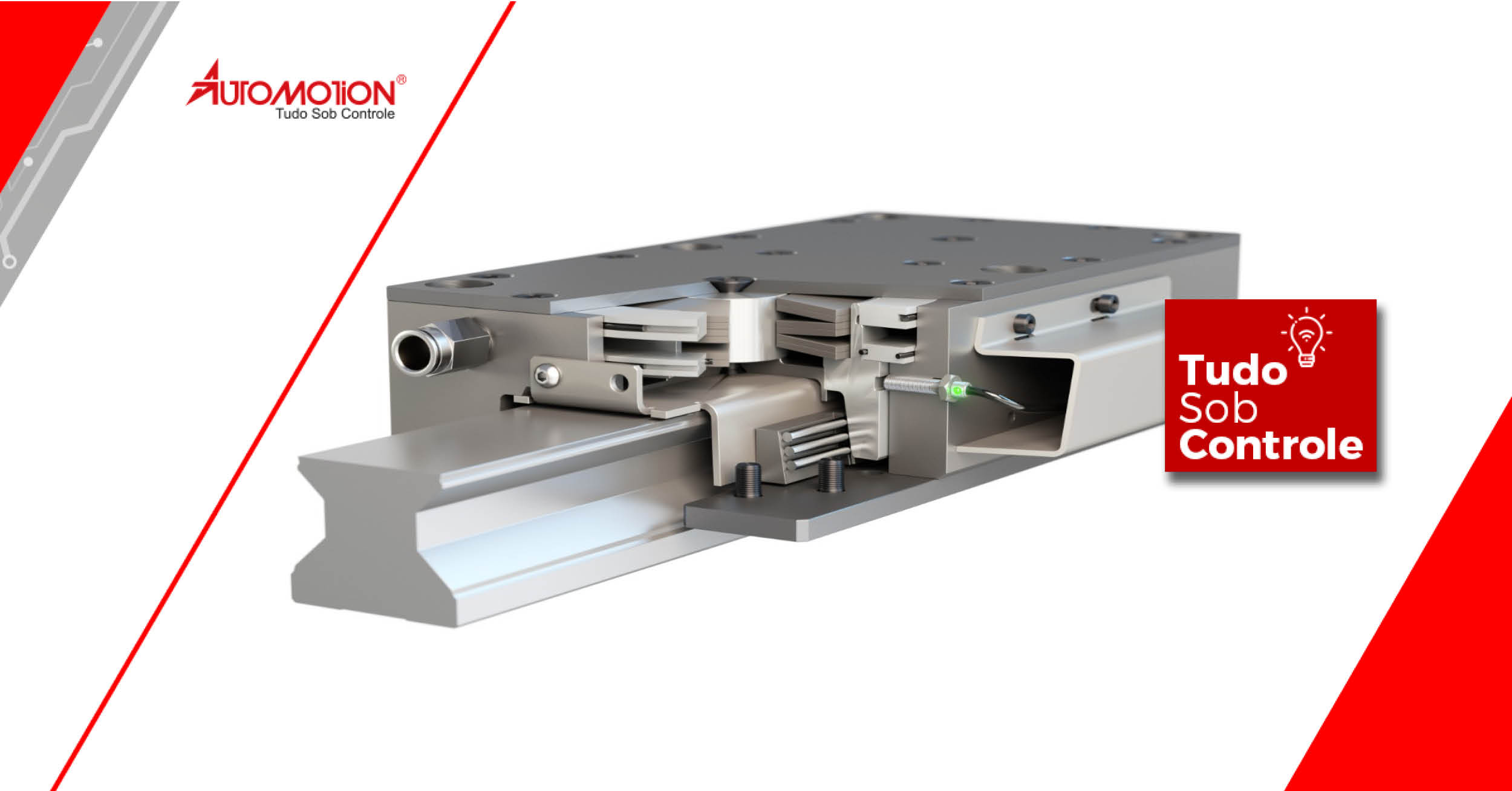
ROBA-Guidestop. Um novo conceito em freio para guias lineares.
A cada dia que passa, a segurança em eixos verticais ganha mais e mais importância, principalmente após a introdução da DIN 13849-1 ou NR12. Com ROBA-guidestop, os movimentos são muito mais seguros e têm maior eficiência energética, além da precisão do processo aumentada e uma superior capacidade de corte. ROBA-guidestop. Inovação a serviço da segurança e eficiência. Todos os países do mundo, em maior ou menor grau, já perceberam a importância de começar, agora mesmo, a caminhada em direção às fontes renováveis de energia. Além de um importante impacto no clima e na qualidade do ar, a economia também é influenciada pelo uso destas fontes diferenciadas de energia. Mas quais são estes impactos? Como eles acontecem? E o que mudarão em nossas vidas? O cenário atual Mas as vantagens de ROBA-guidestop não terminam aí: ele possui importantes componentes para o alívio de tensão e, por isso, proporciona um aumento significativo aumento da vida útil dos eixos em movimento. ROBA-guidestop é um freio hidráulico de segurança que pode ser utilizado diretamente em guias lineares. O freio é integrado ao porte do guia e adaptado ao molde do trilho. As molas pré tensionadas pressionam os revestimentos de fricção no trilho por meio de um arranjo de amplificação de força. A transmissão de força funciona com a completa ausência de folga e é projetada para extrema rigidez. O freio é liberado com pressão de 70 bar e os pistões pressionam contra as molas prato, abrindo as “garras”. Estas molas prato permitem um curso longo e compensam as tolerâncias do trilho, sem nenhuma perda de força ou capacidade de frenagem. ROBA-guidestop é um freio redundante, com sistema de frenagem independente. Com freios no motor, o acoplamento do eixo, os redutores e o fuso de esfera devem ser dimensionados, não só para o torque do motor, mas também para o torque de frenagem, que é geralmente mais elevado. ROBA-guidestop é instalado diretamente no carro entre os dois patins da guia linear e atua diretamente sobre a carga. Assim, além de proporcionar níveis de segurança mais elevados, há o aumento do tempo de vida dos componentes de acionamento, gerando maior economia e reduzindo o número de manutenções preventivas ou paradas emergenciais da máquina. Com ROBA-guidestop é possível alcançar uma rigidez superior a 1000 N/μm. Assim, é possível que, em interação com a carga movida, o controle do motor pode ser “desligado” durante o processo de usinagem, aliviando substancialmente a pressão sobre o fuso de esferas. E dependendo do tipo de usinagem isso significa uma grande economia de energia. Outra vantagem da elevada rigidez tornou-se evidente durante os testes do ROBA-guidestop: ao ser instalado numa máquina protótipo, ele torna a máquina muito mais rígida, permitindo altas capacidades de corte. A máquina também tem sua vibração diminuída e, como consequência, a superfície usinada terá um acabamento melhor. A utilização do ROBA-guidestop garante que os movimentos dos eixos carregados sejam realizados com segurança. Sua construção rígida minimiza as vibrações, melhorando a qualidade de usinagem, aliviando a pressão sobre os componentes de acionamento e ainda proporcionado grande economia de energia ao desligar o eixo.
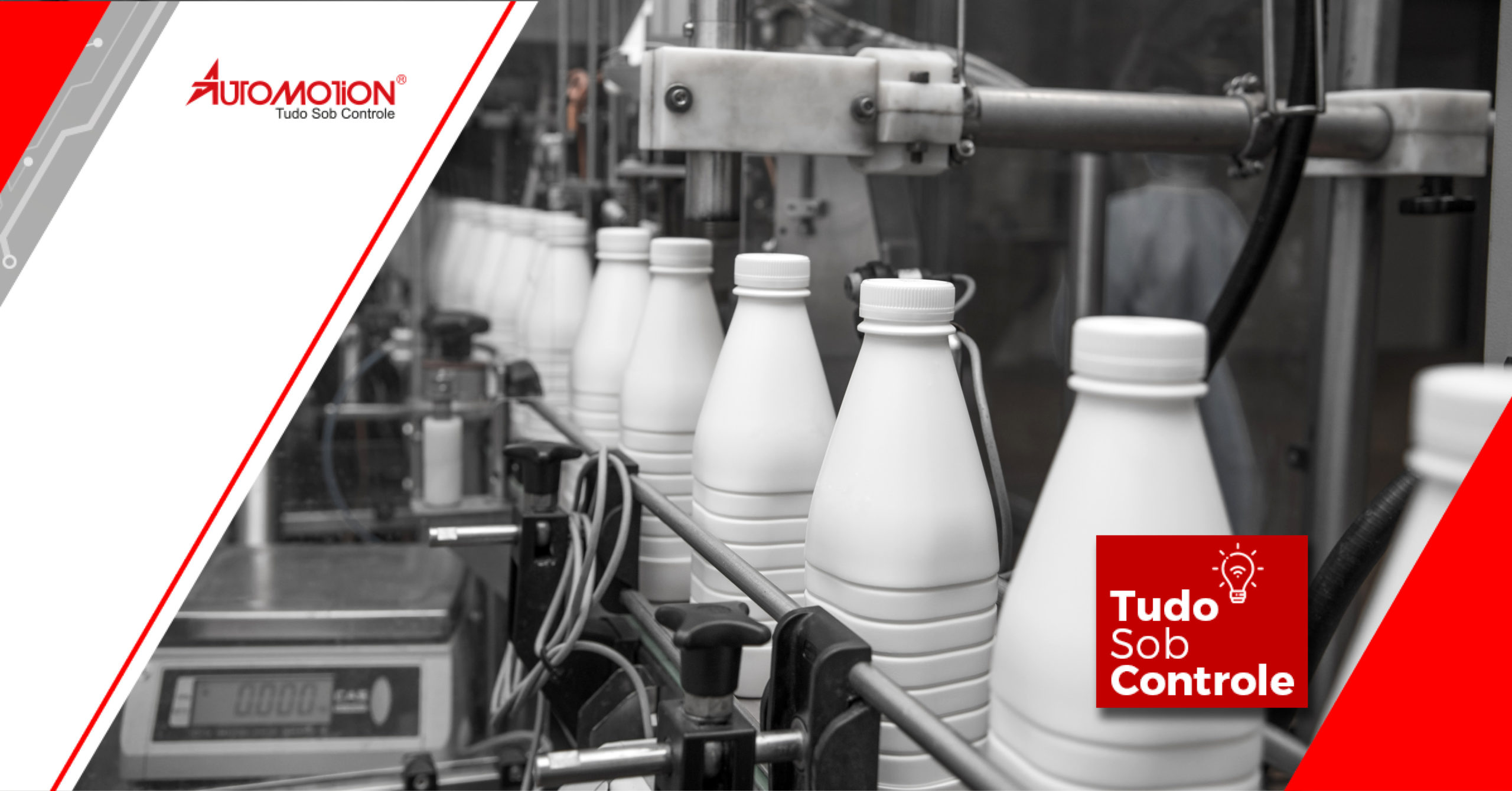
Atuador linear elétrico evita contaminação da linha
Uma das principais processadoras de leite na Suíça que produz diversos lacticínios, incluindo a manteiga, são produzidos nas instalações da empresa em Suhr. Anualmente, a empresa produz mais de 5.500 toneladas de manteiga, entre outros produtos. Mas como os atuadores elétricos entram nessa história de produtividade, e ainda trazendo a economia de energia elétrica? A gente explica esse case de sucesso em detalhes para você. O desafio. Para realizar a dosagem da manteiga no formato correto e na quantidade desejada, era utilizado um sistema hidráulico com uma força de alimentação de aproximadamente 155 kN. No entanto, o sistema hidráulico da empresa deveria ser substituído, pois o uso óleo não era mais recomendado no processo, devido às novas diretrizes de qualidade e segurança, para evitar uma possível contaminação do produto. Além disso, outros objetivos eram motivadores desta substituição: proporcionar uma dosagem mais precisa do produto, ter a certeza de trocas mais rápidas e a garantia de menos manutenção do equipamento. O resultado perfeito não poderia ser outro: uma solução Exlar. Solucionando a questão. E trazendo novas vantagens Para resolver esta questão, atendendo a todos os seus requisitos, que tal uma solução elétrica? Ou melhor, que tal um dispositivo elétrico Exlar? • Os atuadores eletromecânicos Exlar são perfeitos para atender aos requisitos que regem o processamento de alimentos, eliminando a necessidade de sistemas hidráulicos: óleo, bombas, mangueiras e filtros, etc. • Atuadores eletromecânicos garantem maior precisão, mesmo quando atuando com alta repetibilidade. Neste caso específico, o controle total da porção de manteiga pôde ser alcançado. • Os atuadores eletromecânicos são flexíveis; mudanças parciais podem ser feitas de maneira ágil e prática, pois a conversão mecânica ou a recalibração do sistema não são necessárias: basta o usuário selecionar a configuração do produto em uma tabela e o sistema eletrônico faz todo o restante. Rapidamente, ficou claro que uma solução eletromecânica apresentava muitas outras vantagens além da eliminação de óleo utilizado nos sistemas hidráulico. As etapas do projeto. O próximo passo a ser dado foi o dimensionamento. O sistema hidráulico até então utilizado foi monitorado no local para a captura de seus ciclos e o carregamento de seus dados. Este dimensionamento foi fundamental, pois os sistemas hidráulicos geralmente são superdimensionados para lidar com momentos de pico força, que normalmente correspondem a curtíssimos períodos de tempo de sua atuação. Os sistemas elétricos, via de regra, não precisam ser projetados para lidar com a força dessa maneira. Um projeto que leve em conta a força média de produção é suficiente, pois os servodrives podem aplicar uma força de duas a três vezes sua força nominal por curtos períodos de tempo. A carga média cúbica do sistema também foi calculada para dimensionar o fuso de engrenagem planetária para proporcionar a vida útil necessária ao equipamento. Com os dados do sistema anterior (hidráulico) já colhidos e devidamente analisados, um novo sistema, agora totalmente elétrico, foi projetado. Com um sólido e dedicado trabalho, o fornecedor Exlar foi capaz de projetar um sistema perfeitamente suficiente para operar, sem superdimensionamento algum. A prensa de manteiga recebeu um retrofit com um atuador elétrico Exlar FTX215, com força de alimentação de 178 kN. Os atuadores FTX usam a tecnologia de Fusos de Engrenagens Planetárias Exlar. Para gerar a força linear por meio do fuso planetário, é acionado um servo motor com torque de 60Nm. O redutor planetário intermediário com uma relação de redução de 5:1 gera o aumento de torque para 300Nm. Um servodriver de 90 KvA controla o motor. Os Resultados Após o comissionamento no local e realizadas as calibrações mais precisas, a produção na prensa de manteiga foi reiniciada com sucesso. Os benefícios foram muito além da eliminação do óleo: •Precisão na dosagem: redução de 50% nos desperdícios. • Perfis de Movimento Infinito: a velocidade de produção agora pode ser ajustada em tempo real, o que tem aumentando a qualidade. • Tempo de troca reduzido: com o sistema elétrico, não são mais necessários ajustes ou reajustes mecânicos constantes para uma dosagem precisa. Basta apenas selecionar os parâmetros desejados no controle. • Redução Significativa de Ruído: os ruídos de impacto decorrente da partida da máquina e dos batentes mecânicos não ocorrem no sistema elétrico. As vibrações produzidas pelo zumbido hidráulico também foram eliminadas. O novo sistema superou em grande escala todas as expectativas. Mas um dos melhores resultados, de acordo com a própria empresa foi a economia: 60% de redução do uso de energia elétrica. Com crescentes exigências em torno da segurança alimentar, os sistemas hidráulicos são cada vez menos indicados para a indústria alimentícia, devido aos riscos da contaminação decorrente do vazamento de óleo dos equipamentos na linha de produção. Graças às soluções elétricas, os sistemas hidráulicos vêm sendo substituídos pelos sistemas elétrico mecânicos, garantindo uma maior produtividade e, importante, menor necessidade de manutenção. Se você quer conhecer estas e outras soluções para sua linha de produção, entre em contato hoje mesmo com nosso time de especialistas.
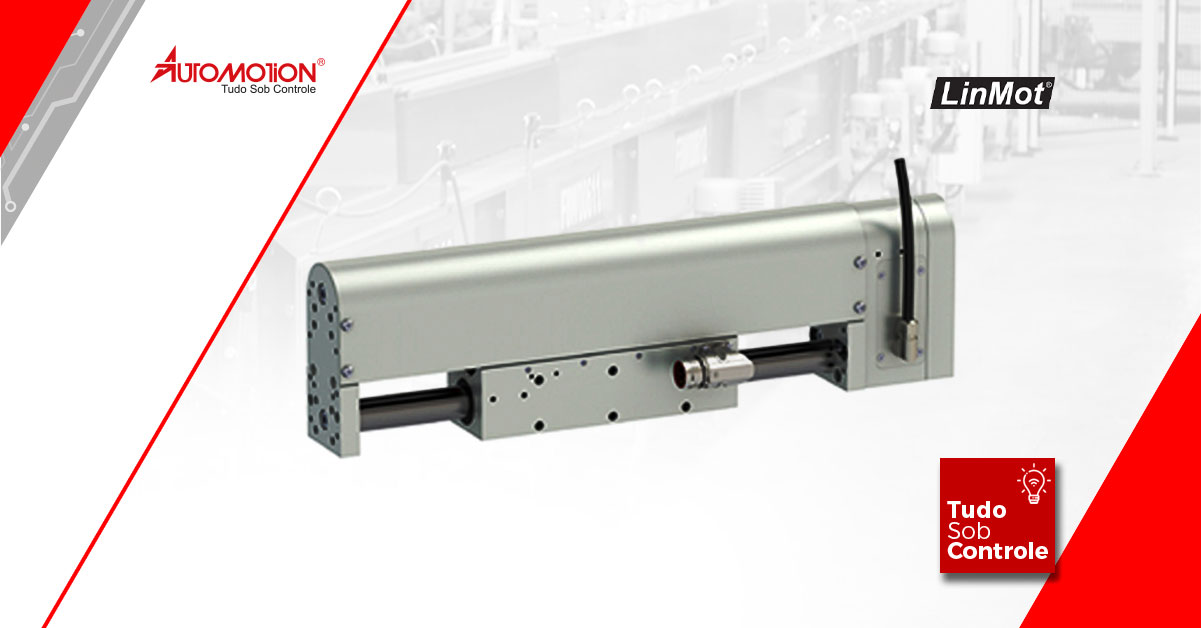
Módulos Lineares DM01
Os módulos lineares DM01 são soluções de acionamento completas que consistem em guia linear e estatores LinMot firmemente integrados e, opcionalmente, “molas magnéticas” MagSpring incorporadas a um freio de retenção pneumático. Eles são acionados por fusos de esfera, correias dentadas, sistemas pneumáticos, acionamentos com cremalheira de engrenagem ou motores lineares. A tecnologia principal dessas unidades de acionamento consiste nos motores lineares PS01-23, PS01-37 e PS01-48 LinMot. Essas opções permitem ao usuário produzir forças de até 572 N, e comprimentos de curso de até 575 mm. As capacidades do motor, com acelerações de até 50 m/s e velocidade máxima de 5 m/s, são capazes de superar com sucesso as demandas de praticamente qualquer aplicação. Veja algumas características do módulo linear DM01: Montagem direta da carga com absorção de forças transversais; Carcaça de alumínio anodizado para fácil limpeza; Hastes-guia resistentes à corrosão, cromadas rígidas; Rolamentos de esferas lineares com lubrificante de grau alimentício (NSF H1); Opção MagSpring® disponível para compensação de carga vertical; Pode ser combinado para formar sistemas de dois eixos. As vantagens dos módulos de sensores de força Os módulos sensores de força das séries DM01-37-FSxx e DM01-48-FSxx podem ser sobrepostos diretamente aos módulos lineares da série DM01 e, assim, possibilitam a medição das forças que ocorrem na direção de movimento dos módulos. Junto com os drives C1250, que também podem ser calibrados, é possível executar um processo de forma controlada por força ou implementar o monitoramento de processo com base nas forças que ocorrem. Listamos aqui os diferenciais DM01-37-FSxx e DM01-48-FSxx: Sobreposição frontal com sensores de força para montagem direta em módulos DM01; Realização de aplicações de força controlada, como junção ou prensagem; Implementação de controles de processo com base em perfis de força; Medição de força desacoplada na direção do movimento independente do ponto de aplicação de força; Montagem arbitrária de garras ou ferramentas sem influência de medição; Alta precisão de medição com alta resistência de sobrecarga simultânea. Mantenha os ambientes livres de contaminantes Os guias DM foram desenvolvidos para garantir estabilidade confiável e a limpeza na produção. Os módulos lineares DM são certificados como componentes para aplicações em salas limpas. Ideais para a indústria alimentícia e farmacêutica, eles estão: Disponíveis com certificação de sala limpa até ISO4; Equipados com lubrificantes seguros para alimentos. Escolha as melhores soluções de automação industrial para a sua empresa, fale com o time de engenharia da Automotion! Clique aqui e verifique a viabilidade desse projeto na sua empresa.
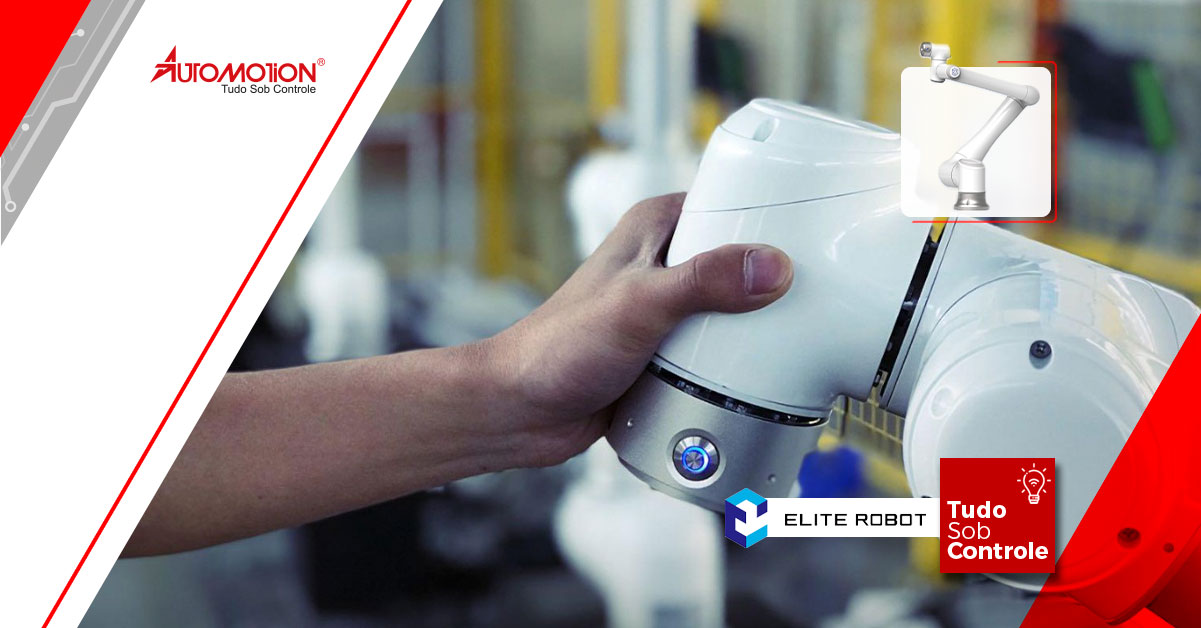
Robôs colaborativos para paletização
O robô colaborativo realiza tarefas lado a lado com os colaboradores da empresa, elevando a produtividade, a eficiência, a segurança e qualidade dos processos produtivos. Por serem totalmente fechados, eles não contêm servomotores, cabos ou outras partes expostas, diferentemente dos robôs industriais convencionais aos quais faltam funções de segurança integradas. Além disso, estruturas convencionais necessitam de vários dispositivos de segurança para evitar o acesso do operador com o robô em ciclo automático. Sendo assim, o robô colaborativo tem como um dos diferenciais a facilidade na integração em linhas de produção onde layout seria um problema para um robô convencional, portanto, a velocidade do startup dos colaborativos acaba sendo um ponto importante ser considerado. Desafios da paletização – Facilidade, flexibilidade e automação Na linha de produção existem vários trabalhos feitos manualmente pelos colaboradores. A paletização, por exemplo, exige que os colaboradores transportem cargas pesadas para montar o palete durante todo o turno de trabalho. Isso pode causar problemas de saúde, porque os trabalhadores giram constantemente a cintura, causando problemas posturais e desgastes pelo esforço repetitivo. Do ponto de vista econômico, os lotes de produtos estão mudando constantemente, exigindo técnicas de produção mais flexíveis. Consequentemente, a linha de produção atual deve ser capaz de produzir vários tipos de produtos em grandes lotes. É justamente no processo de automatização das máquinas que se torna fundamental incluir esse requisito para deixar os equipamentos mais fáceis de operar, flexíveis para implantar e seguros para trabalhar em colaboração com os trabalhadores. A solução de automação convencional é substituir o trabalho humano por robôs industriais tradicionais. Na entrada e saída da linha de produção, robôs industriais são instalados para realizarem a despaletização e paletização, além de entregarem materiais para a linha de produção ou montarem produtos acabados para embalagem. O problema com os robôs industriais é que, uma vez que o espaço da linha de produção é levado em consideração, haverá algumas limitações, incluindo àquelas de estruturas da fábrica, como espaçamento entre colunas e algumas vezes até o teto baixo. Uma vez que a célula com robôs industriais tradicionais é implantada, seu layout não pode sofrer grandes ajustes e muitas vezes sequer poderá ser alterado. Obviamente, essa solução não atende uma célula de manufatura flexível que precisa atender diferentes lotes e alterações de tamanho e volume do produto acabado. Robôs colaborativos que garantem velocidade e segurança no processo Os nossos robôs colaborativos flexíveis e compactos compartilham o espaço de trabalho com as pessoas e têm grandes vantagens. O palete padrão tem 1,2m² e a altura após completo é de 1,8m. Os robôs fixos no espaço e que atendem aos requisitos serão os robôs industriais que pesam centenas de quilos. Por conta do grande peso, grande volume e instalação de grade de segurança, a dificuldade em adaptar o layout da linha de produção muitas vezes torna o projeto inviável. Embora o alcance do robô colaborativo não seja capaz de atender aos requisitos de altura, por ser leve e flexível na instalação, utilizar uma coluna elétrica torna possível atender a última camada do palete sem espaço adicional. Isso garante o aumento da eficiência geral na produção e segurança dos colaboradores. O robô colaborativo EC612 tem alcance de 1304 mm e carga útil máxima de 12 kg. Ele atende a velocidade da linha de produção, mantendo a segurança no processo. É possível adicionar a função de gravar a trajetória do robô colaborativo através da programação no Teach Pendant. Na prática, quando a produção trocar o lote do produto ou alterar tamanho, pode escolher o programa predefinido e ajustar os pontos para permitir que o robô comece a trabalhar de acordo com as novas dimensões da camada. A melhor maneira de avaliar as aplicações destes robôs e dimensionar o melhor custo x benefício para a sua empresa é consultando um time de engenharia especialista em soluções de alta produtividade que são adaptáveis a pequenos espaços. Fale com o time de engenharia da Automotion agora mesmo e saiba mais.
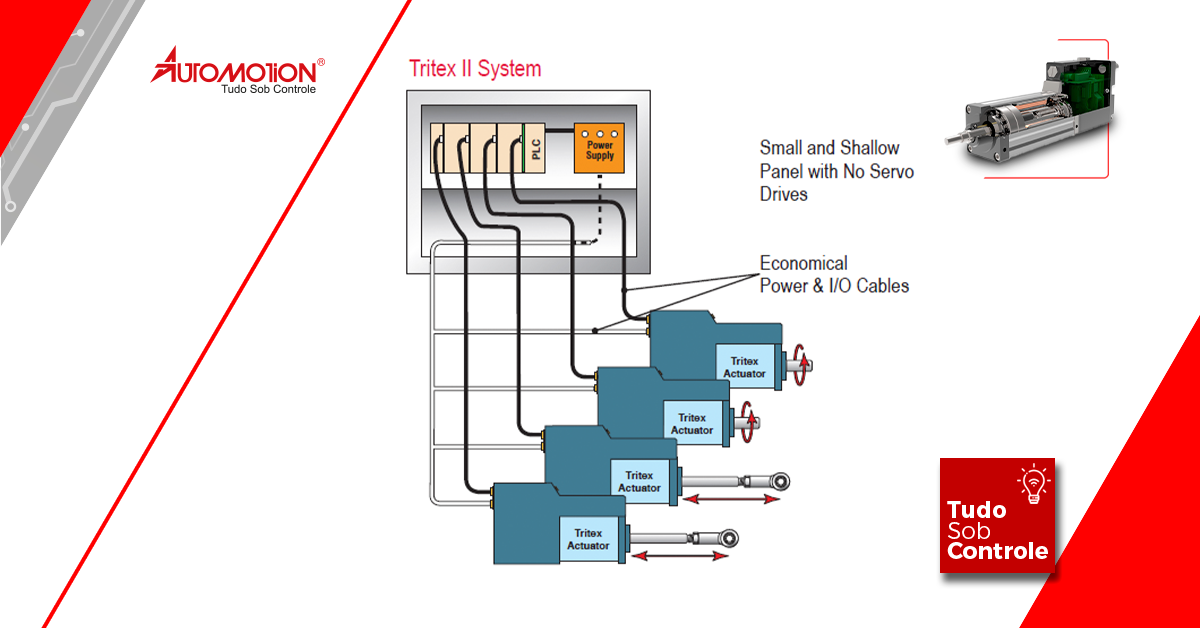
Por que escolher os sistemas elétricos?
Uma ampla indústria demanda por maior eficiência e maior rendimento, sendo assim, o eletromecânico é uma alternativa atraente para substituir os cilindros com fluido hidráulico. Se você fabrica máquinas para terceiros ou precisa de uma solução para esta substituição, a atuação elétrica oferece diversas vantagens que superam o sistema hidráulico. Eficiência energética Os sistemas elétricos possuem eficiência em torno de 80%, enquanto os sistemas hidráulicos são somente 50% eficientes. Estes sistemas hidráulicos exigem pressão e força constantes para manter a posição. Os sistemas elétricos, por sua vez, podem ser configurados para extrair energia apenas em movimento. Os resultados são notáveis: 60% de economia de energia, podendo financiar o retrofit completo de um sistema hidráulico para o sistema elétrico. Segurança, Saúde e Manutenção Fluidos hidráulicos são caros e exigem substituição constante, além de eliminarem resíduos perigosos. Uma solução elétrica é naturalmente mais limpa, ecologicamente correta, além de segura para o seu trabalho. O risco de segurança de vazamentos de óleo em alta pressão é completamente eliminado, assim como o risco de incêndio devido a óleos inflamáveis, pois não há mangueiras de óleo ou vedações para vazar e reparar. Por isso, os sistemas elétricos são mais vantajosos, especialmente por exigirem pouca manutenção. Entre outras vantagens, estão os níveis de ruído: eles são 30% mais baixos. No geral, a preservação da saúde e prevenção dos riscos de segurança por si só tornam o sistema elétrico uma valiosa solução. Instalação / facilidade de uso Sistemas elétricos são muito mais fáceis de instalar, porque os cabos de conexão rápida são instalados em uma pequena fração do tempo que leva para encanar um sistema hidráulico inteiro. Atuadores eletromecânicos Exlar® oferecem uma verdadeira experiência “plug-and-play” em qualquer configuração que você precisar: • apenas atuador • motor / atuador integrado • acionamento / motor / atuador integrado. Além disso, o tamanho físico de um sistema elétrico é muito menor do que um sistema hidráulico, devido à eliminação de pacotes de energia, filtros, bombas, válvulas e reservatórios, minimizando sua instalação e economizando em equipamentos. Precisão combinada à flexibilidade A precisão e controle do sistema elétrico oferecem maior flexibilidade, qualidade e vida útil à ferramenta. Taxas de ciclo mais altas podem ser alcançadas por meio de tempos de reação mais curtos, comparando-se elétrica versus sistemas hidráulicos. A sua produção terá estabilidade aprimorada em toda a instalação e melhor repetibilidade em faixas de temperatura. Os sistemas de atuadores elétricos não sofrem com os mesmos problemas que a hidráulica, como a mudança de temperatura. Maior precisão, programabilidade, flexibilidade e confiabilidade! Quer saber como isso é possível? Fale com a equipe de engenharia da Automotion agora mesmo e saiba mais!
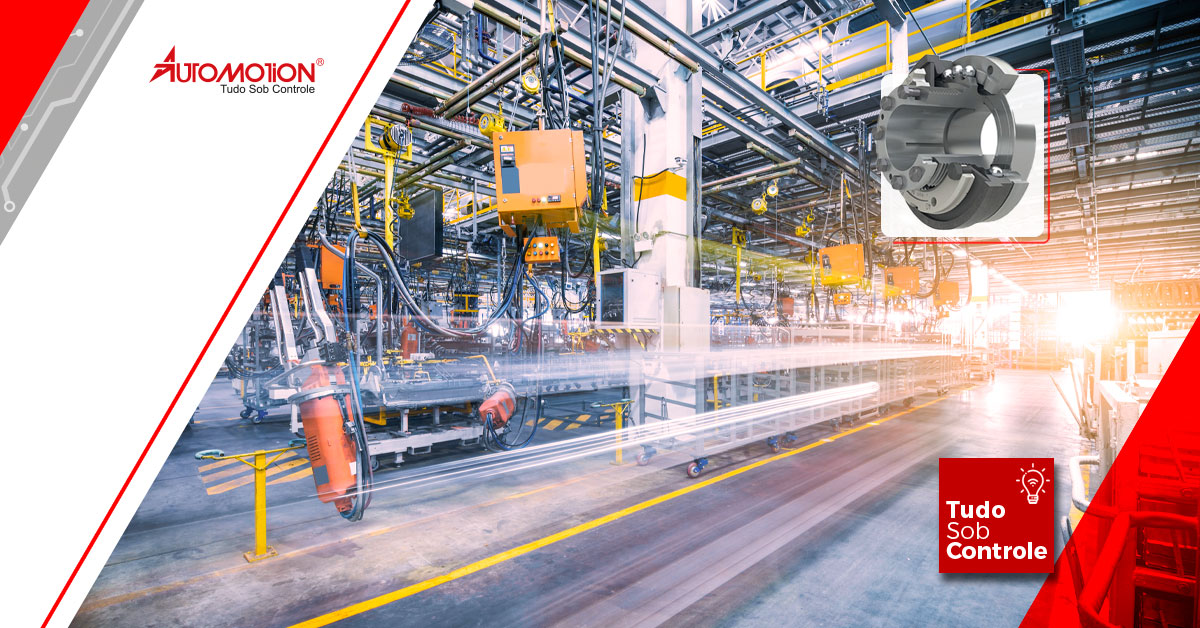
Limitadores de torque: Evite quebra de componentes
Danos e falhas de produção devidos à colisão são caros e prejudiciais para a imagem da empresa, sendo assim, é melhor se eles puderem ser evitados. Durante o desenvolvimento de drives inteligentes, estratégias eletrônicas surgiram em paralelo às soluções mecânicas para a prevenção de sobrecargas. A embreagem de sobrecarga mecânica permanece indispensável. O princípio de operação de uma proteção mecânica, por sua vez, é baseado na separação da entrada e saída e na fragmentação da energia na linha de transmissão. Como resultado, as cargas que atuam na posição de colisão podem ser reduzidas significativamente. Além disso, as embreagens de sobrecarga podem realizar qualquer tempo de reação curto desejado, pois um elemento passivo é incorporado ao design que se ajusta às condições na linha de transmissão. Simulações em bancadas de testes especiais comprovam que uma proteção eficaz contra sobrecarga só é possível com limitadores de torque. As embreagens garantem o bom funcionamento das máquinas e ferramentas e, consequentemente, um processo de produção sem interrupções. Os limitadores de torque e força da Mayr® Power Transmission protegem máquinas e sistemas de forma confiável contra danos de sobrecarga dispendiosos. As chamadas embreagens sobrepostas também ajudam a aumentar a produção e a produtividade por meio da redução do tempo de inatividade. Desde o conceito de design até a produção em volume, os produtos Mayr® Power Transmission são totalmente suportados por documentação, incluindo modelos CAD, desenhos 2D, instruções de operação e fichas técnicas, a maioria das quais pode ser baixada diretamente no site da empresa. A embreagem limitadora de torque certa para sua aplicação Seja um modelo que patina, como os limitadores de torque por atrito, ou que desacopla, como o modelo por esferas, as embreagens de sobrecarga Mayr® são caracterizadas pela mais alta qualidade e por uma transmissão de torque particularmente livre de folga. Estas embreagens limitadoras de torque são à prova de ferrugem e particularmente robustas. As embreagens limitadoras de torque são usadas em uma ampla variedade de aplicações: 1) Tampas para fechamento de garrafas ou movimento de giro em máquinas de envase; 2) Para limitar as forças de tração e compressão; 3) Como limitadores de torque também para aplicações de alta velocidade e aplicações pesadas; 4) Transportadores de cargas; 5) Bancadas de testes; 6) Mineração; 7) Máquinas e ferramentas. Saiba mais sobre os limitadores de torque esfera assistindo o vídeo a seguir:Limitador de torque esferas EAS Compact – Mayr Fale com a equipe de engenharia da Automotion agora mesmo e saiba mais sobre esta tecnologia que pode evitar danos e prejuízos para sua indústria.
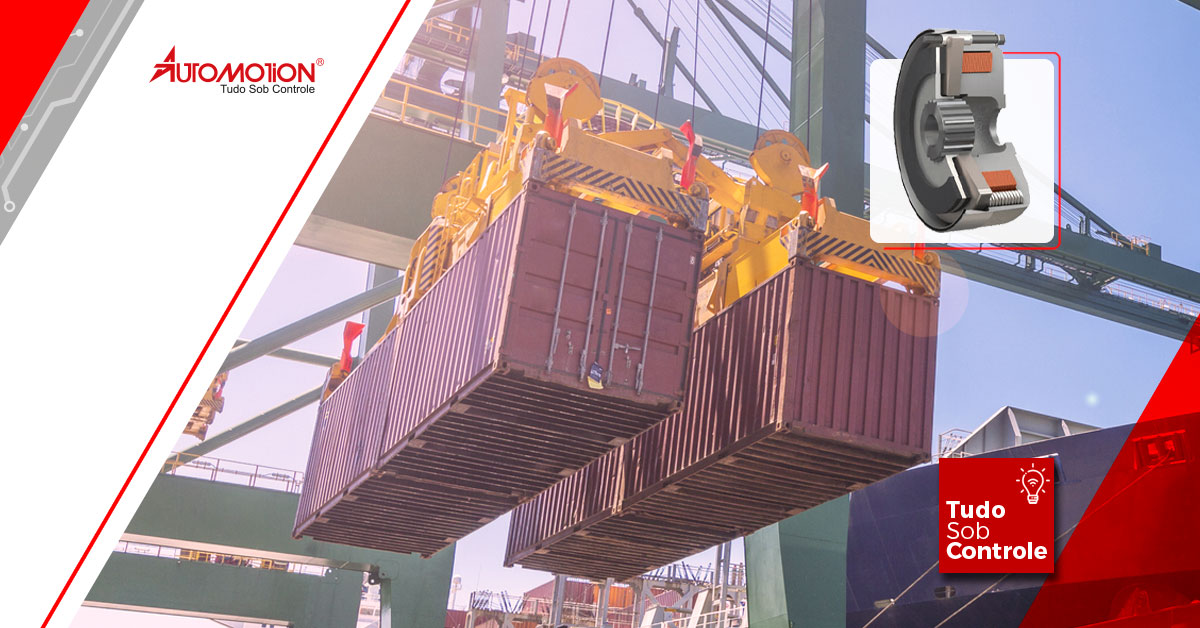
Sistemas de freio para guindastes e aplicações de içamento
A construção de guindastes, guindastes portuários, pontes rolantes e guinchos de cabo deve ser realizada de forma confiável e com qualidade, especialmente quando possui pessoas sob as cargas. Os freios de segurança oferecidos pela Mayr®Power garantem retenção confiável e segura durante a operação normal. Contudo, eles também são projetados para absorver picos de carga com extremo trabalho de alta fricção em uma emergência. Para aplicações externas e condições ambientais críticas, a Mayr desenvolveu um freio de segurança totalmente à prova d’água e poeira que pode suportar as altas cargas. Além dos freios, as embreagens e acoplamentos Mayr®Power também auxiliam nos sistemas de guindastes e aplicações de içamento. Conheça algumas opções de freios e suas vantagens para cada tarefa e setor. Freios de segurança para carrinhos e guinchos em pontes rolantes Em salas de produção, pontes rolantes transportam material e peças de A a B – às vezes, sobre máquinas – e, em alguns casos, as pessoas também podem estar nas proximidades. Por este motivo, os freios de segurança ROBA-stop®-M são usados nos carrinhos e talhas das soluções de guindastes. Esses freios são projetados para instalação na extremidade do eixo livre, garantindo a retenção confiável e desacelerando massas ou cargas em movimento. Em caso de parada de emergência, falha de energia ou mau funcionamento, os freios ROBA-stop®-M seguram qualquer posição e, portanto, evitam quedas ou colisões descontroladas. Isso não apenas protege os funcionários de lesões, mas também o material, peças e máquinas de danos. Freios externos robustos para guinchos de convés e guindastes de navio Seja para âncoras, botes ou redes de pesca, os freios para guinchos a bordo de navios são usados para uma ampla gama de tarefas. Além disso, guindastes de navio também são usados para içamento e transporte material. Neste caso, os freios de segurança robustos são adaptados às condições ambientais do clima marítimo, bem como projetados para frenagem de emergência com cargas de pico e altas, sendo necessários trabalhos de fricção. Com a transmissão de energia ROBA-stop®-S, a Mayr® desenvolveu um freio de segurança especialmente para condições ambientais críticas e externas. Ele está em conformidade com os requisitos de proteção IP67 e, portanto, totalmente à prova de poeira e à prova d’água. Além disso, os freios ROBA®-stop-M atendem aos projetos de construção e a alta proteção IP 66 relacionada ao design selado. Freios de segurança confiáveis para talhas de corrente, talhas de cabo de aço e talhas de correia As cargas também são frequentemente transportadas com talhas de corrente, talhas de cabo de aço e talhas de correia em aplicações industriais, bem como em teatros, óperas e concertos. Estes dispositivos da maquinaria superior precisam se mover para manter decorações de palco ou unidades de iluminação acima dos atores ou cantores durante uma performance, por exemplo, ou eles também podem transportar pessoas. Isso requer segurança especial e requisitos a serem cumpridos. Os freios de segurança nas unidades têm um papel importante: em uma emergência, eles devem salvar vidas. Em caso de falha de energia ou parada de emergência, eles param as cargas o mais rápido possível para evitar ferimentos pessoais ou danos à propriedade. Como sistemas de freio, os freios de circuito duplo operam completamente independentes um do outro. Cada um dos dois freios também é capaz de segurar a carga com segurança por conta própria, protegendo, assim, de forma confiável, os atores no palco de peças em queda em caso de emergência. Com os freios de estágio ROBA-stop®, a Mayr® Power Transmission desenvolveu dispositivos que são redundantes, mas ainda funcionam sem dobrar o torque de frenagem em caso de parada de emergência. Isso significa que eles freiam suavemente e de uma maneira que seja gentil com os componentes – a carga de acidentes é, portanto, significativamente reduzida. Os freios atendem a todos os requisitos de segurança da norma DIN EN 17206. Se você quer saber como esta tecnologia aplica-se na sua indústria, fale com o time de engenharia da Automotion agora mesmo.